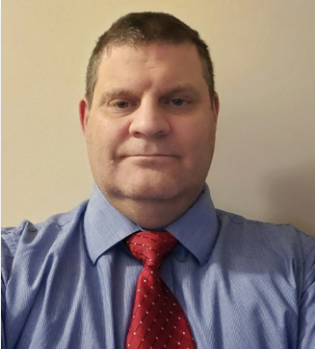
2023 OSHA Update
Topic Area: OSHA
Level: Intermediate
DESCRIPTION: This class is designed to present to the audience current and future initiatives, programs, and regulatory agenda for FY23 and looking ahead to FY24. It will discuss current Region 1 Local Emphasis Programs (LEPs) and Regional Emphasis programs. The class will feature a look at the R\LEPs enforcement, data trends in these programs and proposed changes (if applicable) to them.
Speaker: Brett Fortin – Compliance Assistance Specialist with the Springfield Area OSHA office
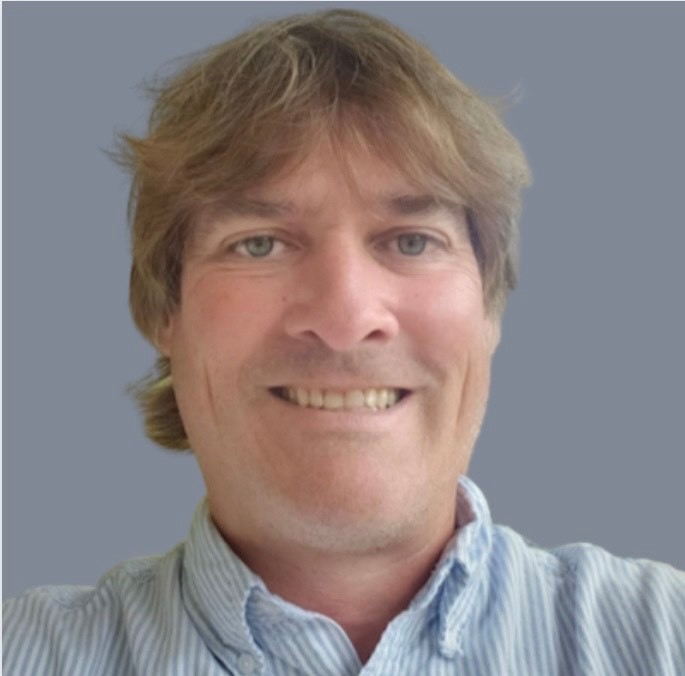
Behavior Based Safety Programs & Employee Involvement
Topic Area: VPP Element – Management Leadership & Employee Involvement
Level: Basic
DESCRIPTION: This presentation will look at the Behavior Based Safety Program that Veolia uses to encourage manager commitment and employee involvement and participation.
The presentation will review the following:
- The four elements of VPP including Management Leadership and Employee Involvement
- What behavior-based safety is and the benefits of the program.
- The development and continuous improvement of Veolia’s behavior based program
- The integration of Veolia Leading Indicators website and Intelex.
- Veolia’s Report It Don’t Ignore This (RIDIT) safety incentive program.
- Results of the Participation for 2022.
Speaker: Rich Finnegan – EH&S Manager, SGE, Vice Chair, Region II VPPPA; Veolia, Marlboro, MA
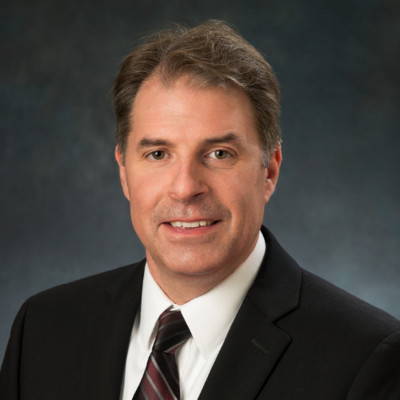
Implementing Human & Organizational Performance (HOP) with the Expanded Event Factors Chart (EEFC) for Incident Reviews
Topic Area: VPP Element – Worksite Analysis
Level: Intermediate
DESCRIPTION: This presentation will describe how the Collins Aerospace Windsor Locks site has started applying Human & Organization Performance (HOP) principles with the use of a tool called the Expanded Event Factors Chart (EEFC) as part of our event reviews. HOP (also called the “New View” in some circles) is a movement towards using the social sciences to better understand how to design resilient systems. One of the most conceptually tricky aspects of HOP is that it is not a program. The New View is a philosophy which, when adopted, creates a local culture change that leads to better system design. HOP is a science-based approach helping us identify issues in our systems impacting workers to better address them more effectively. It builds an understanding of how humans perform and how we can build systems that are more error tolerant.
Speaker: Matt Twerdy – Director, Site EH&S, Collins Aerospace, Windsor Locks, CT
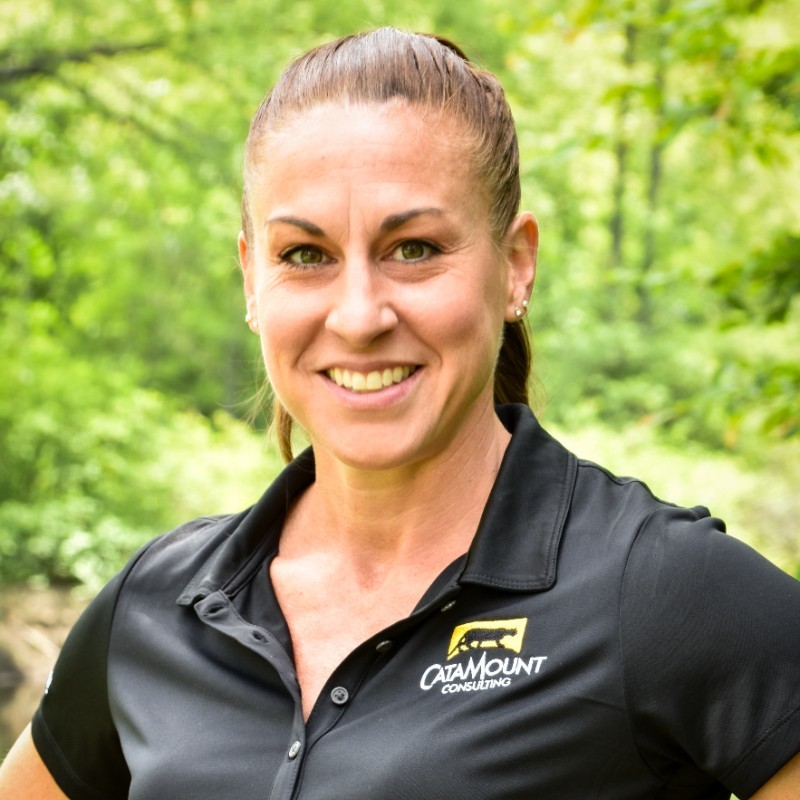
Safety – “It’s all in your head”
Topic Area: VPP Element – Management Leadership & Employee Involvement
Level: Basic
DESCRIPTION: Are rules and regulations most effective at creating safer workplaces or is it “All in our Heads”? The answer to this question is an astounding YES! While standards and procedures are paramount, the key to safer workplaces and jobsites lies in understanding leadership and how it influences the 6-inch space between our ears. Let’s take off our hard hats for this session and get to know our brains and provide our teams with tools and strategies to be more connected, motivated, present, and emotionally agile.
Speakers: Stacy Spector, Scott McKenna, Jason Spector – Catamount Consulting, LLC, Warrensburg, NY
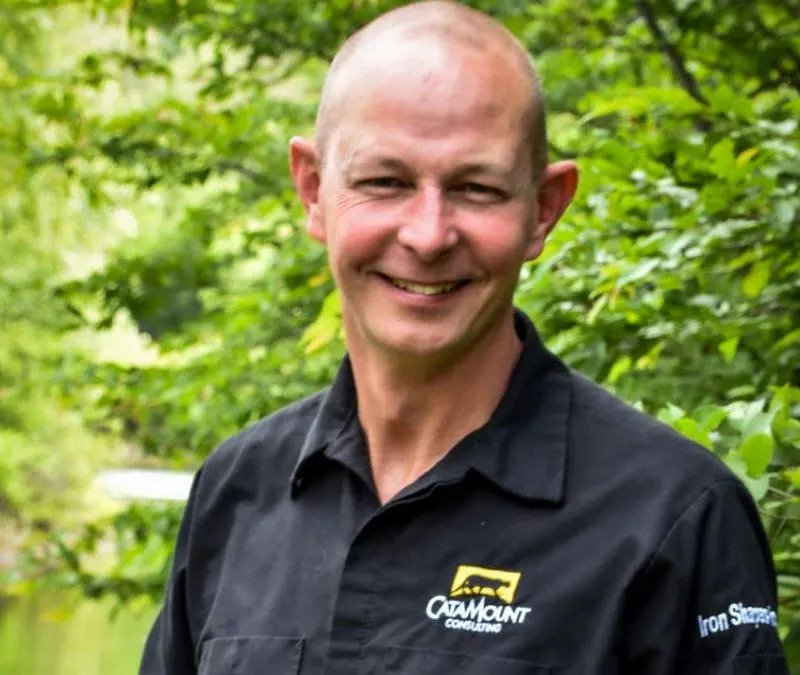
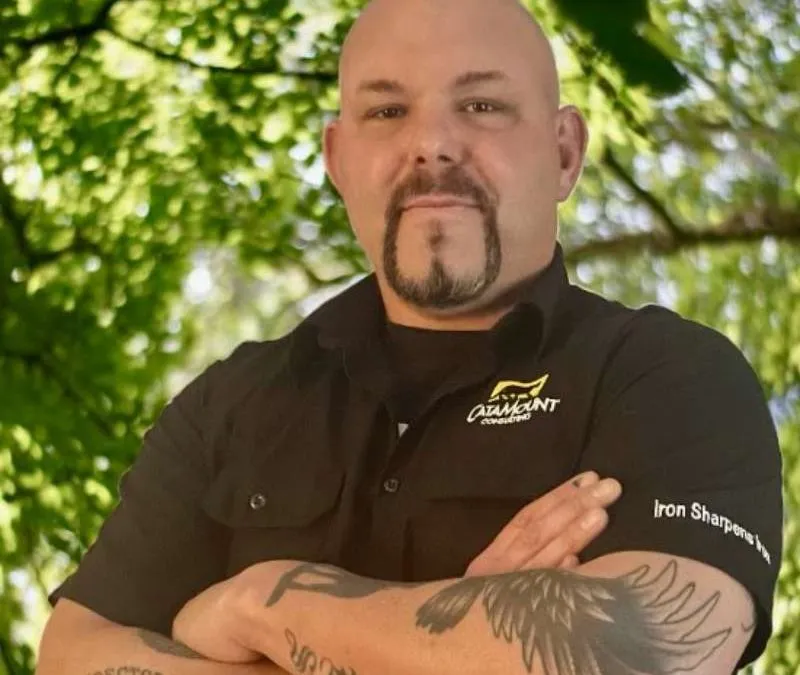
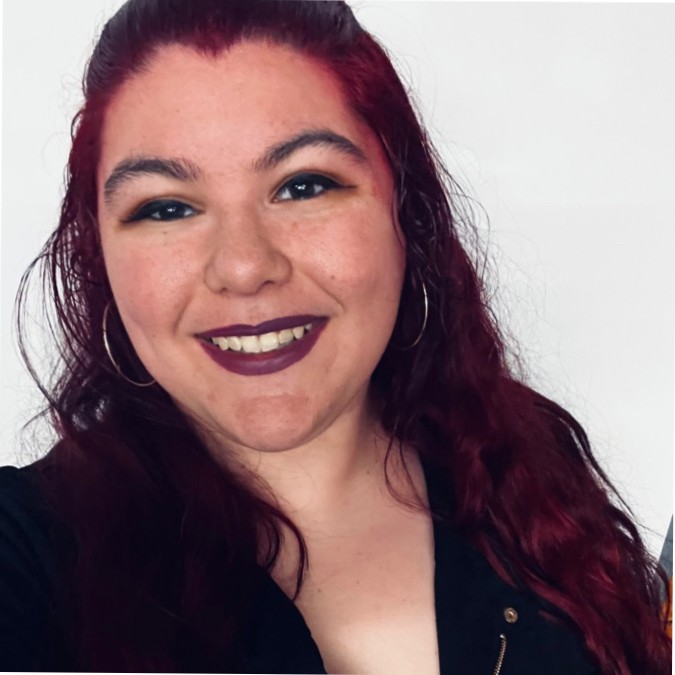
Take what you need. A collection of Best Practices and Engagements to help corporations strengthen their safety programs and support VPP initiatives.
Topic Area: VPP Element – Management Leadership & Employee Involvement
Level: Basic
DESCRIPTION: A STAR VPP worksite presents a collection of tested and successful Engagements and Best Practices to inspire corporations to strengthen their safety programs and support VPP initiatives. Attend and take only what you need; additional resources available, discussions are encouraged.
(Presenter will have prepared handouts for attendees to take with them.)
Speaker: Nina Mendonca – VPP Coordinator, Chatham Village Foods (A Division of T. Marzetti Distributions), Wareham, MA
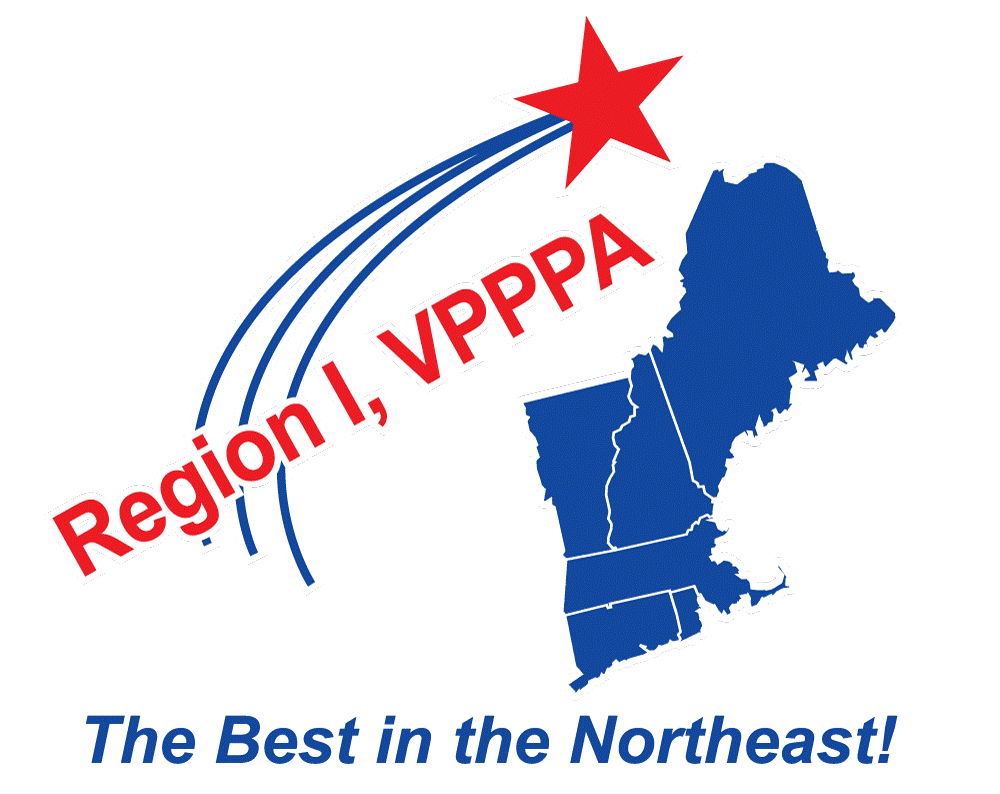
Controlling electrostatic within hazardous atmospheres
Topic Area: VPP Element – Hazard Prevention & Control (Static Bonding and Grounding)
Level: Intermediate/Advance
DESCRIPTION: Electrostatic charge is an unfortunate by-product of many processes within industry. If discharge occurs within a hazardous atmosphere, the resulting spark may easily act as the ignition source for an explosion. To increase awareness of the problems, and to propose practical solutions, Newson Gale to attendees who are serious about tackling their static issues.
Outline of session:
- Introduction
- Assessing electrostatic hazards:
- Could there be a flammable atmosphere?
- Can charge be generated?
- Can charge accumulate?
- Could there be a spark risk?
- Is there enough energy for ignition?
- Static control measures:
- Bonding and grounding
- Minimizing charge generation
- Maximizing charge dissipation
- Case Study
- Conclusion
Speaker: Peter McMenamin – Northeast, US and Southeast, Canada Regional Manager, Newson Gale, Marlborough, MA
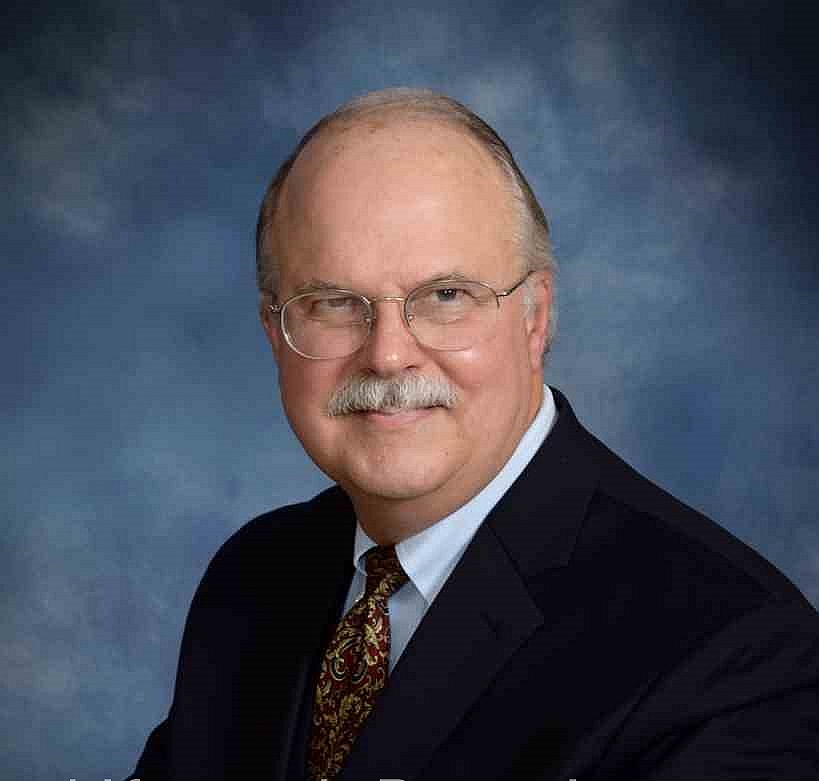
“Competent Person Safety Specialist” a delivery multiplier in a general industry safety program
Topic Area: VPP Element – Management Leadership and Employee Involvement
Level: Intermediate
DESCRIPTION: Best Practice Sharing an underutilized asset – The OSHA defined “Competent Person” its empowerment as a Safety Specialist: A how-to application of this resource at an industrial facility. A force multiplier for hands-on safety program sustainability.
Speaker: Brad Bittenbender – Jacobs Engineering Group, Inc. (liaison to GE Lynn site engineering group), Wrentham, MA
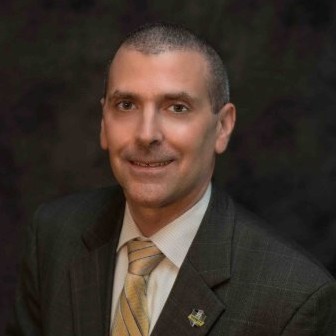
Creative Confidence
Topic Area: VPP Element – Management Leadership and Employee Involvement
Level: Intermediate
DESCRIPTION: Teambuilding and creative collaboration. Courage is calling us to make a difference within our organizations, while continuously evolving our strategies in new innovative ways to constant changes that help to add value while maximizing impact and returns. Learn about the Human Centered Design (HSD) process at https://www.designkit.org/human-centered-design.html.
Speakers: Frank V. Ragone and Jeff Gut – Cintas Corporation
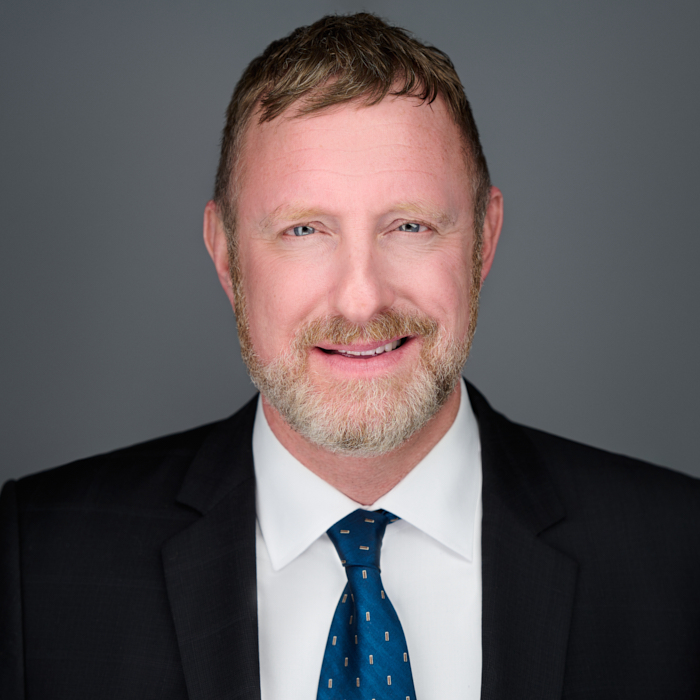
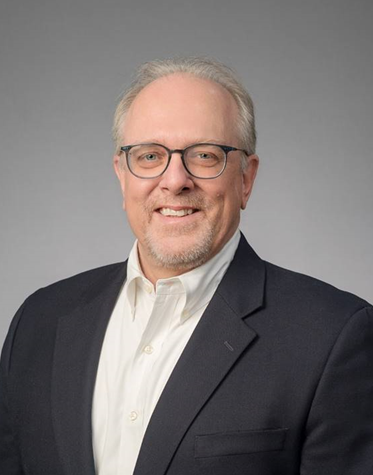
“Highs, Lows and Plateaus”
Topic Area: VPP Element – Management Leadership and Employee Involvement (sub-element: Contractor Management)
Level: Basic
DESCRIPTION: Safety Culture maturity highs and lows as well as the dreaded “Plateau”. David Beck and John Mullen will review the Windsor Locks Contractor Safety Program to talk about how they are extending their site Safety Culture to their Contractor work force.
Speakers: John Mullen – Sr. Project Manager – Fuss & O’Neill Manufacturing Solutions, LLC
David Beck – Sr. Health & Safety Manager – Collins Aerospace, Windsor Locks, CT
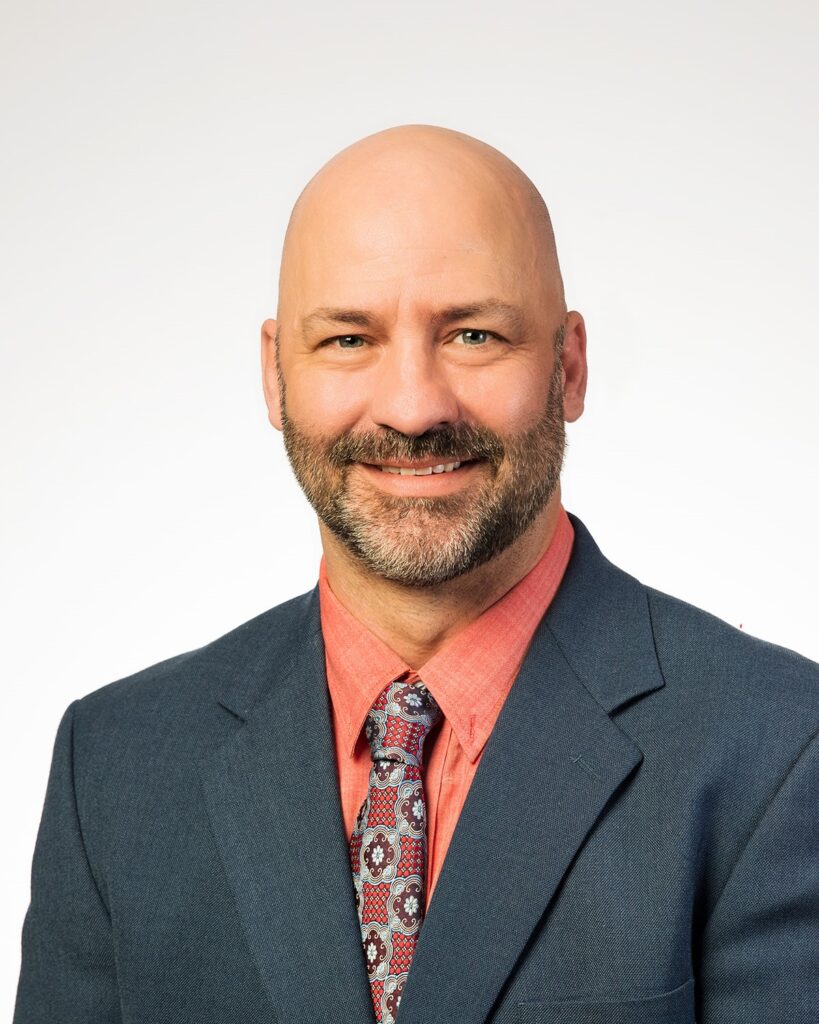
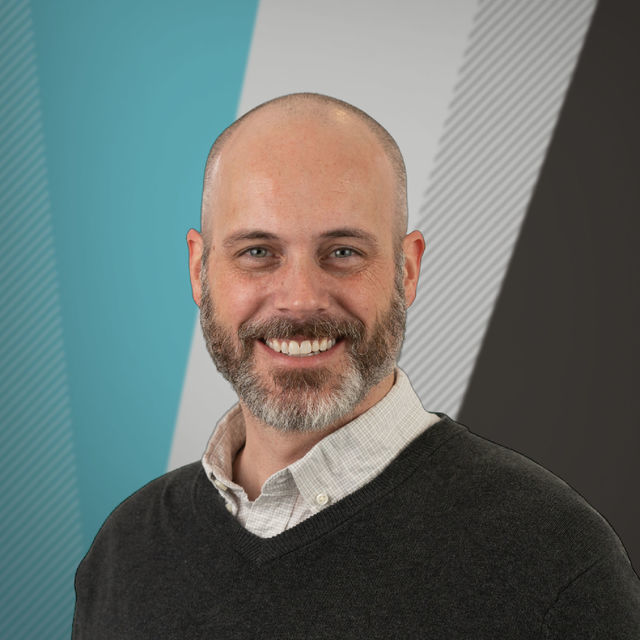
People – The Problem or the Solution?
Topic Area: VPP Element – Management Leadership and Employee Involvement
Level: Intermediate
DESCRIPTION: In a worldview where people are the problem, the role of the safety professional is to find and fix problems (people or conditions). In a worldview where people are the solution, the role of the safety professional is to support people in coping with complex work situations (people in the conditions). There are a lot of implications there for practice and Ron will discuss in detail the opportunities to balance fixing and supporting. Fixing is loaning someone money. Supporting is going through their finances with them to help them figure out how to pay bills now and in the future (working the system). Creating dialogue helps a group analyze and understand their problem so they can learn from what is going on to create better more long-term impactful solutions.
Speaker: Ron Gantt – HSE Director for the Americas for Yondr Group
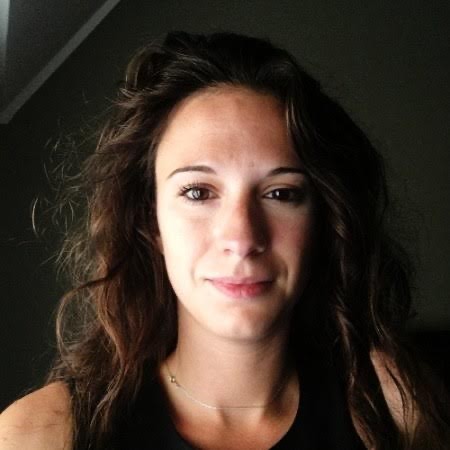
HOP (Human and Organizational Performance) the New View – Accountability in Resilient Design
Topic Area: VPP Element – Management Leadership and Employee Involvement
Level: Intermediate
DESCRIPTION: If we are punished for X, we don’t stop doing X, we try to avoid getting caught. So, when an event occurs, we need to ask better questions that move us past the biases we have towards error and blame. We learn an error was made or a rule was broken, but we also learn how the error was made and why the rule was broken. We recognize we would have probably made a similar error or broken the same rule if we were doing the job, which in turn lets us acknowledge that the failure will inevitable be repeated unless we improve. Our employees become our biggest asset in improving the system and we end up with a long list of possible improvement actions. Our working relationships and ability to solve problems improves.
This session will help explain how HOP fits into the world of accountability. One of the largest hurdles to adopting a HOP lens is understanding how “strategically choosing to learn and improve” (Conklin) fits within the frame of accountability. Join for some stories and guidance along this path.
Speaker: Andrea Baker – The “HOP Mentor” (Human and Organizational Performance)

Report It Don’t Ignore It (RIDII)
Topic Area: Engagement
Level: Intermediate
DESCRIPTION:
Management, labor, EH&S, and OSHA work cooperatively and proactively at the Collins Windsor Locks site to prevent injuries and illnesses through a system focused on: hazard prevention and control; worksite analysis; training; and management commitment and worker involvement. The Windsor Locks population of over 4,000 view safety as a fundamental value in all daily actions.
This presentation will describe how Collins Aerospace Windsor Locks has implemented their Hazard / Near Miss Reporting program, Report It Don’t Ignore It (RIDII), for the past 20 years as a cooperative program with the site Union and Management resulting in a culture of psychological safety where employees feel they can express themselves without consequences.
A culture of psychological safety is one in which employees share the belief that it is safe to articulate ideas, raise concerns or express disagreement. Research confirms that organizational effectiveness is positively impacted when employees feel psychologically safe to make meaningful contributions. (Culture Change Consultants).
The RIDII program is a system that can be used by all employees to report safety hazards, concerns, and opportunities for improvement. Reporting these opportunities can proactively prevent injury, illness, property damage and environmental impact.
Benefits:
- Strengthened safety culture through the encouragement of proactive reporting of EH&S issues and hazardous conditions.
- Increased awareness and employee involvement, including communication of corrective actions.
- Decreased probability of serious injuries.
- Enhanced access for reporting through desktop shortcut links.
As part of the program, there is a process to follow up with the submitter and track corrective actions until completion. Feedback is sent to the submitter, providing confidence that the hazard has been addressed.
Speaker: Bruce Gove, Chief Union Safety Representative, Region 1 Board Member
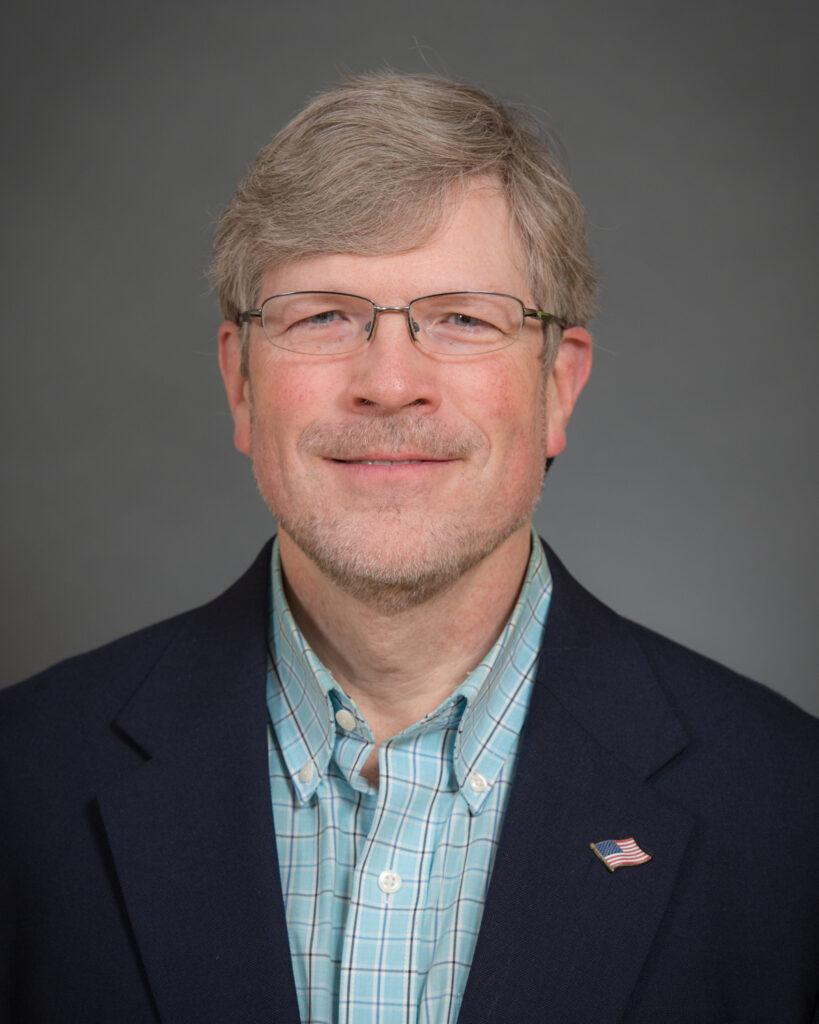
Ergonomics for Dummies (A Fun and User-Friendly Way to Demonstrate Ergonomic Principles for Our Team)
Topic Area: Ergonomics
Level: Basic
DESCRIPTION: Have you always wanted to become more ergonomically savvy, but never knew where to start? Join us for Ergo for Dummies, a fun and interactive crash-course that can help you in your workplace. Learn how to banish backaches, wave goodbye to wrist strain, and embrace the art of ergonomics! Let’s dive into the world of happy spines and pain-free productivity. So in the future, when someone asks you about Ergonomics, you can smile (outside and in) and say, “Let’s Go Ergo”!
Speaker: Jeff Stolz, Director-At-Large, Nominations Committee Chair
CCA Operational Excellence Manager
Raytheon Technologies

Safety Game Time – Using and Creating Games to Educate, Challenge and Inspire our Team
Topic Area: Engagement
Level: Basic
DESCRIPTION:
In this dynamic, highly interactive presentation, we will play games and learn how to create them! After we play each game, we will work together to develop an understanding of the hows, whys and outcomes of each game type. We will have fun seeing opportunities to use these games to challenge our team to raise our level of safety excellence. After we have mastered these concepts, we will work to learn how we can develop our own games to target the specific safety training objectives of our team.
Please join us in a fun, interactive, dynamic presentation that will forever change how you think about ‘playing to win’!
Speaker: Jeff Stolz, Director-At-Large, Nominations Committee Chair
CCA Operational Excellence Manager
Raytheon Technologies